Dipl.-Ing. Dr. Bernhard Aschenbrenner
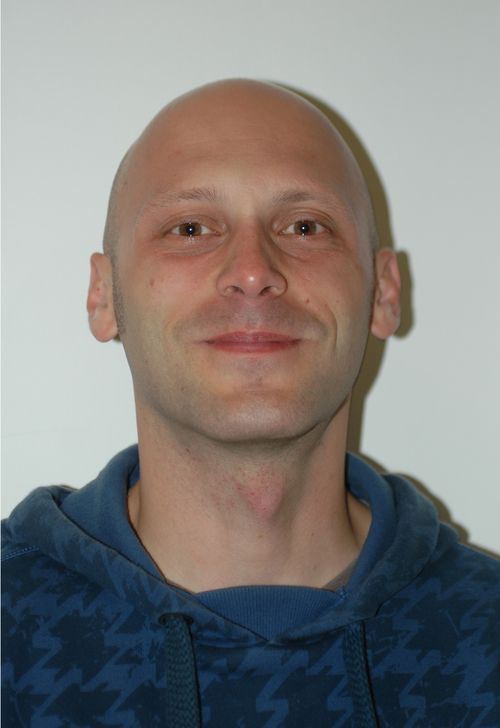
Supervisory Committee: | |
---|---|
Univ.-Prof. Dipl.-Ing. Dr. Bernhard Zagar | |
Final exam: | |
July 14, 2015 |
Supervisory Committee: | Univ.-Prof. Dipl.-Ing. Dr. Bernhard Zagar |
Final exam: | July 14, 2015 |
The objective of this research was to develop a novel absolute angle sensor technology which is applicable for through-shaft applications.
The sensor has to be narrow enough to be integrated in a ball bearing cap.
SKF Österreich AG, opens an external URL in a new window approached the Austrian Center of Competence in Mechatronics, opens an external URL in a new window (ACCM) to conduct this research.
The sensor works on principles similar to contactless resolvers.
It bases on printed circuit board technologies and its working principles rely on mutual inductive coupling.
Thus, the sensor only consists of a planar excitation coil and position sensing coils formed by conductive tracks on a narrow antenna PCB, which is illustrated in Figure 1, and a detached target PCB which is a passive resonant serial RLC circuit illustrated in Figure 2.


Furthermore, this position sensor is suitable for rough industrial environments, offers a high inherent resolution, can measure target position over a wide measurement range, and can potentially measure multiple target locations simultaneously.
The basic position resolution is improved by adding two additional finer pitched position sensing coils.
The sensor provides amplitude modulated or phase modulated target position dependent output signals.
Furthermore, mathematical models for both cases are derived and discussed in detail.
The use of coupled resonances enables to overcome the weak coupling between the excitation coil and the target coil.
A Cramer-Rao lower bound analysis was performed to evaluate the minimum achievable uncertainty of the position reading.
The amplitude modulated positioning sensing coils signals were demodulated and transformed to a discrete time representation by utilizing bandpass sampling. A novel absolute angle measurement system for large trough shaft applications was introduced and discussed in detail. A notable advantage of this angle measurement principle is that the axial antenna PCB arrangement allows using the same antenna PCB for different shaft diameters. Furthermore, a test-bench was designed to evaluate the measurement performance of the developed angle measurement system. The test bench measurement results of an inductive large diameter through-shaft angel measurement sensor were presented and analyzed in detail.
Keywords: Inductive Position Sensor, Coupled Resonances, Through-Shaft, Bandpass Sampling, Cramer-Rao Lower Bound, Absolute Position Measurement, Printed Circuits
The circulation of the project work is restricted from June 13th, 2015, for a period of 5 years.